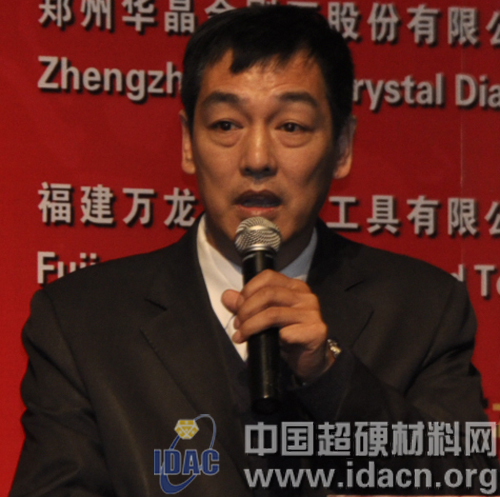
Combined application characteristics and development trend of metal prealloyed powder
The combined application of different types and different particle size metal prealloyed powders has distinct characteristics, especially the combination application of fine particle alloy powders. The combination of fine particle atomized alloy powder and iron-copper alloy prepared by chemical one-step method can greatly improve the comprehensive mechanical properties of the sintered product and improve the sharpness and service life of the tool. The combined application of fine particles and high-activity alloy powders will be the future development trend, and functional combination can be realized to simplify the production process and promote the development of the industry.
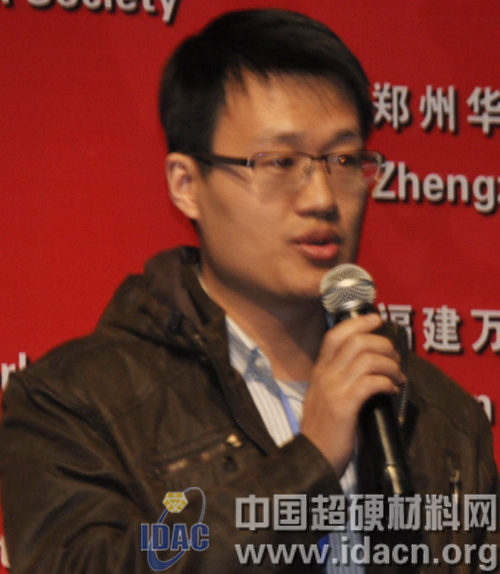
Application of DFC25 Prealloyed Powder in Diamond Tools
The report studied the cold pressing and hot pressing sintering properties of DFC25 prealloyed powder, and analyzed the properties of sintered body hardness and bending strength. The results show that the hardness and flexural strength of DFC25 prealloyed powder increase with the increase of sintering temperature. When the hot pressing temperature is 780 °C and the pressure is 20 MPa, the hardness of the sintered body is 52HRB and the flexural strength is 748MPa. The powder is applied to the production of circular saw blades, and the cutting speed and life of the saw blade can be substantially reduced, and the amount of precious metals such as copper and nickel can be greatly reduced, and the manufacturing cost of the tool can be reduced, compared with the single-mixed powder carcass. At the same time, the tooth strength of the cutter head is significantly improved, which improves the safety of the saw blade.
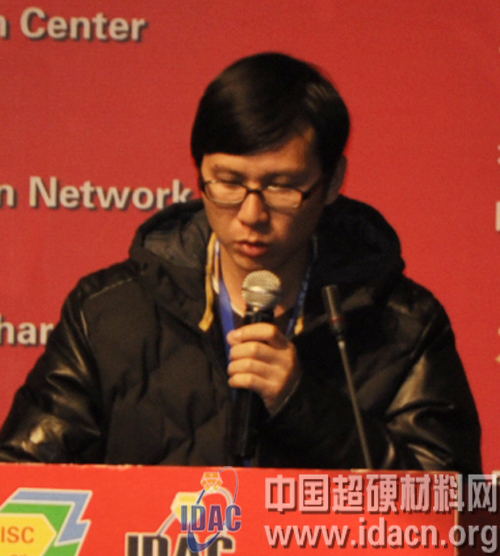
Effect of Sub-nano Prealloyed Powder on Performance of Diamond Tool Carcass
By adding different proportions of sub-nano prealloys in the metal matrix, the effects of the prealloyed powder on the metal matrix density, hardness, flexural strength and the holding power of the diamond were analyzed, and the base metal matrix was added and joined. The comparison of the diamond metal carcass cutting shows that the performance indexes of the carcass added with the sub-nano prealloyed powder are greatly improved, which is close to the performance index of the metal carcass with a certain amount of diamond, and can replace the metal carcass to a certain extent. Part of the drilling powder, in order to more effectively and economically improve the performance of diamond tools.
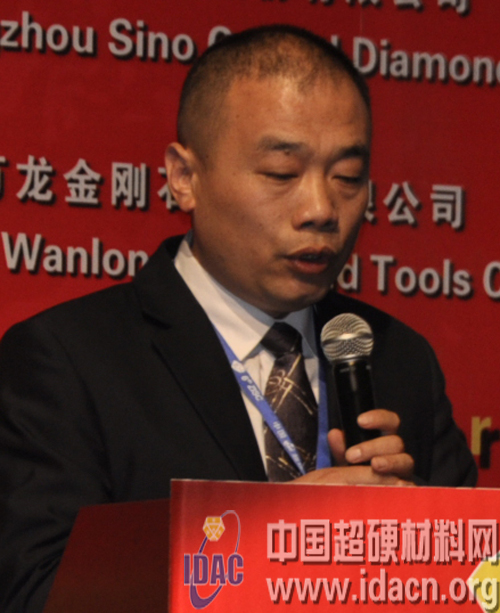
Application of water atomized iron-copper prealloyed powder in medium-diameter granite saw blade
The water atomized iron-copper prealloyed powder JF-O1 with different mechanical properties was selected, and the influence of bending strength and sintering hardness on the cutting performance of the prepared granite saw blade was investigated. When the oxygen content of the prealloyed powder is less than 3000 ppm, the higher the bending strength of the powder sintered body, the better the sintering density of the corresponding saw blade carcass, the higher the bending strength, and the stronger the mechanical holding power of the carcass to the diamond. The sharpness and service life of the saw blade can be significantly improved within a suitable range of sintering hardness.
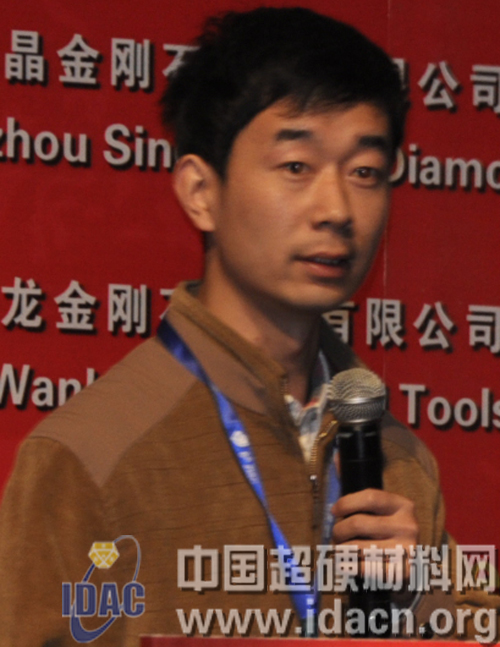
Fractal Analysis of Micro-crushed Morphology of Brazed PCBN
The report mainly carried out the grinding test of the brazed PCBN abrasive tool, and reconstructed the abrasive wear morphology by fractal method. The fractal analysis of the abrasive crushing behavior was carried out. The main conclusions are as follows:1. During the grinding process, the self-sharpening effect caused by the micro-crushing behavior of PCBN can be reconstructed by 3D video microscope. The obtained model can clearly reproduce its wear characteristics. 2 Fractal dimension and PCBN micro-crushing behavior Relevant, thereby quantitatively characterizing the self-sharp effect produced by the micro-crushing behavior of PCBN.
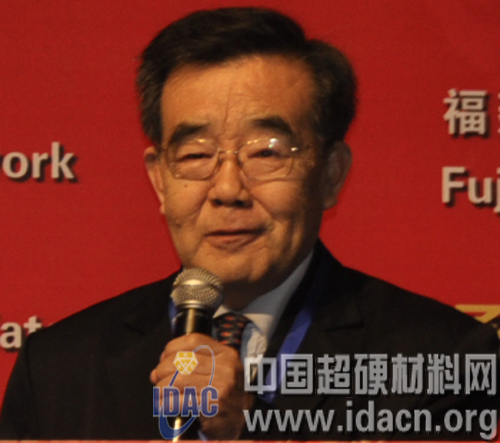
Carcass properties and pre-alloyed powder
The report proposes five characteristics of the diamond tool carcass, namely wear resistance, high grip, strength safety, low-temperature sinterability and good compaction, and explains their technical meanings, and for the carcass The main production methods of prealloyed powder, including water atomization method, coprecipitation reduction method, mechanical crushing method, diffusion alloy method, etc., were observed and analyzed. The powder morphology, particle size and alloy phase greatly affect the five characteristics of the carcass. Pre-alloyed powder is used as the carcass. Due to the complete alloying of the sintered structure, fine grain structure and compact structure, the wear resistance, holding property and safety strength of the carcass are improved; while the sintering temperature is significantly reduced. Amorphous powder is used as a carcass to save energy, reduce production costs and improve tool efficiency.
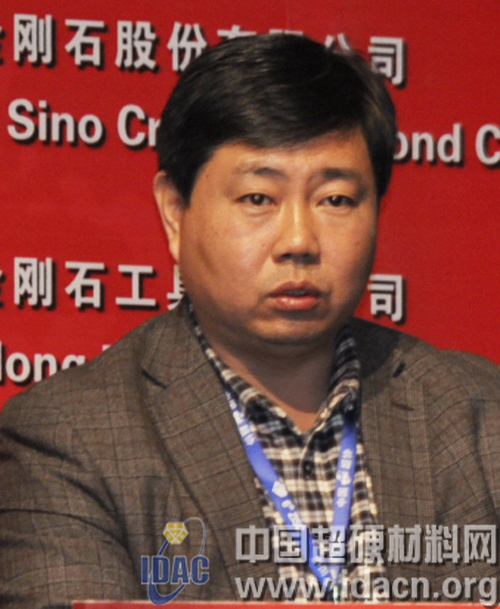
Successful trial of high efficiency vacuum brazing single layer CBN grinding wheel
In this report, a single-layer vacuum brazing CBN grinding wheel was developed. The vacuum brazing process was used to introduce TiH2 into the Cu-based brazing material for experimental analysis. The effects of different brazing temperatures on CBN were compared, and the CBN abrasive grains were properly exposed. In the state of height, the thermal damage and stress damage are fully reduced, and a strong and effective metallurgical combination between the CBN abrasive grains, the brazing material and the 45# carbon steel substrate is achieved, and the high-efficiency grinding of the vacuum brazing CBN grinding wheel is further realized. cut.
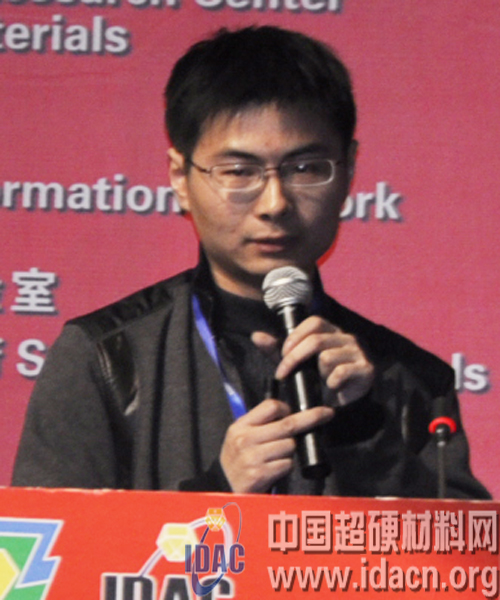
Experimental and Simulation Study on Grinding Temperature of Single Layer Brazed CBN Grinding Wheel 20CrMnTi
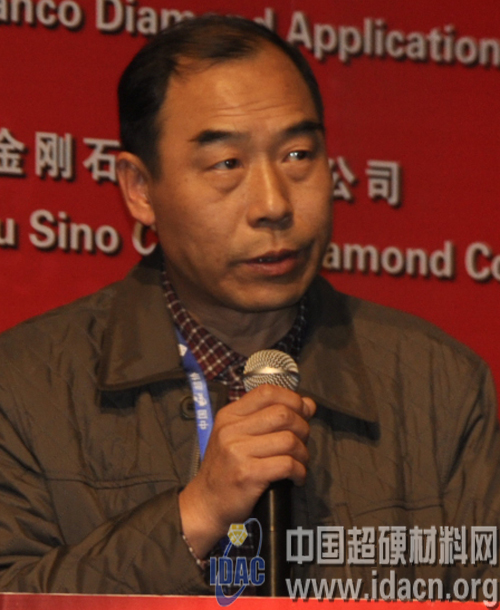
Making superhard material tools by vacuum brazing
The report explains the advantages of superhard material brazing tools. By explaining the technical points of the vacuum brazing equipment and the development factors of the brazing operation process, it is further explained how to make superhard material tools by vacuum brazing.
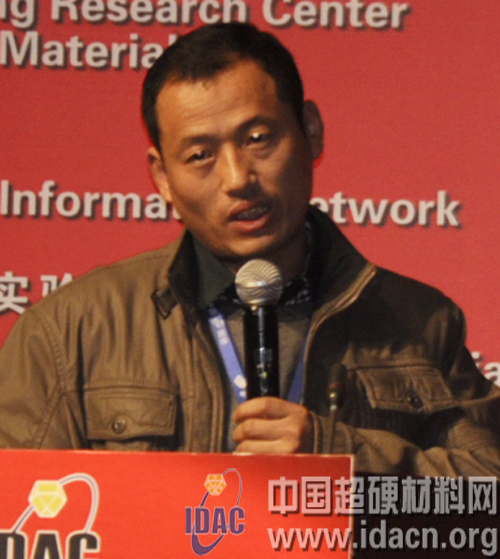
The report uses a vacuum brazing process to prepare a multi-layer diamond drill bit using a nickel-based or copper-based brazing material according to the slit-inlaid structure, and performs a granite drilling test. The statistical analysis method is used to summarize the thickness of three kinds of cutter heads (0.8mm, 1.2mm, 1.6mm) and three kinds of gap spacing (0.8mm, 1.2mm, 1.6mm) and nickel-based and copper-based solders. Failure of 18 multi-layer diamond drill bits. The results show that the nickel-based and copper-based brazing filler metal have achieved a firm combination of diamonds; the multi-layer diamond drill bit brazed with copper-based brazing material has excellent self-sharpness under the condition of 1.2mm cutter head thickness and 1.2mm gap spacing. High sharpness and longer service life.
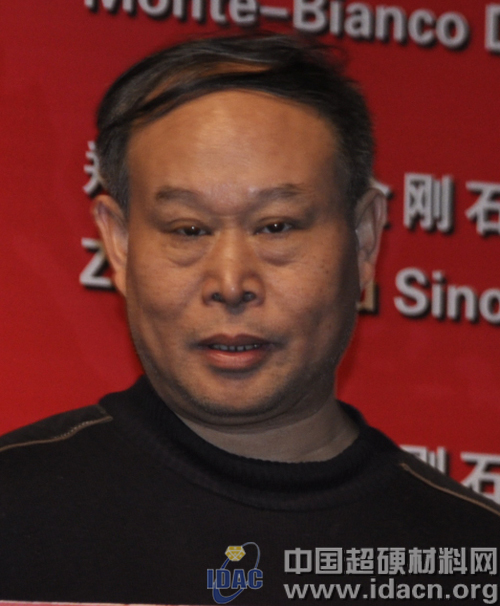
Characteristics and applications of nano ceramic bond
The report comprehensively discusses the performance characteristics of N68-N83 series nano ceramic bond, key technical indicators and application development of ceramic bond superhard tools. It is pointed out that the ceramic bond superhard tool has the advantages of adjustable structure, good self-sharpness, long wear life, no pressure-free sintering in the air of protection atmosphere, and high-volume production in large quantities. The nano-ceramic binder solves the long-term contradiction of low melting and high strength. The sintering temperature is as low as 680 ° C, and the flexural strength of the binder is higher than 100 MPa. According to the requirements of different tools, it can be sintered at a temperature range of 680-850 ° C, and the porosity is 0~95% range adjustment; suitable for diamond and CBN tool manufacturing in the 60-mm to W0.5 full-grain range.
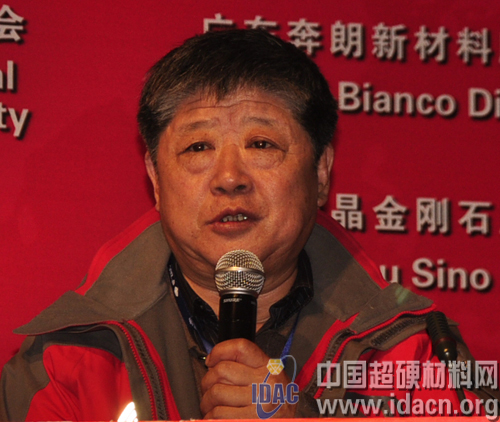
Researcher of Northeast Heavy Machinery Institute, Vice President of Hebei Superhard Materials Association, Director of Yanshan University National Material Comprehensive Experimental Teaching Demonstration Center: Wang Mingzhi
Study on Ceramic Bonds Suitable for Dry Cutting of PCBN Tools
The report is aimed at the requirements of high hardness, high wear resistance and thermal stability of PCBN materials for dry cutting tools. Through the preparation of TiNo.3/AlN/CBN composite sintered bodies, SEM, EDS, XRD and other analytical methods were used to obtain all PCBN consisting of CBN, TiN0.3, TiNx and A1N has no low melting point and low hardness phase, which solves the low temperature sintering problem of covalent bond compounds such as TiN, AlN, etc., and lowers the sintering temperature; through the bonding agent and PCBN Performance testing to match the performance of the PCBN bond to dry cutting tools.

Effect of filler on the performance of resin diamond grinding wheel
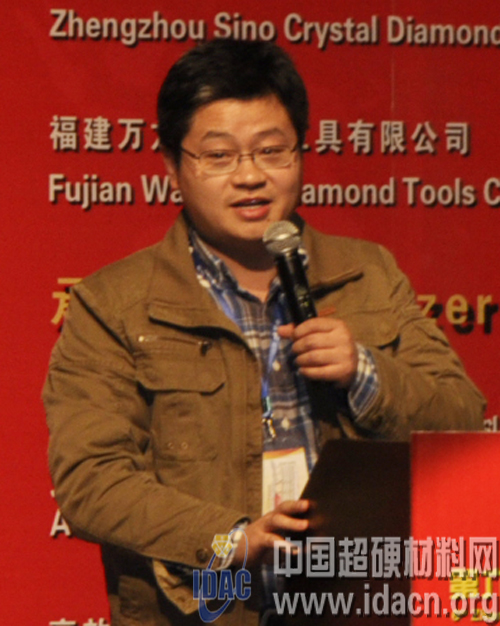
Effect of the addition amount of ZnO on the properties of ceramic bond
This report examines the effect of the amount of ZnO added on the properties of ceramic binders. The experimental results show that the refractoriness of the binder decreases with the increase of Zn0 content; when the addition amount of Zn0 is more than 4 wt%, the refractoriness of the binder is not obvious. The addition of 4 wt% of Zn0 can cause a significant decrease in the expansion coefficient of the binder. The addition of Zn0 also provides a certain increase in the flexural strength of the binder.
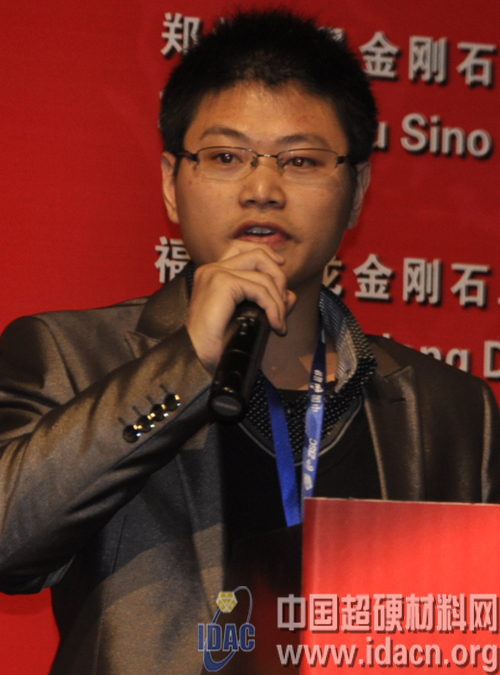
High-end carbide saw blades for grinding woodworking saw blades
This report classifies the diamond grinding wheel used in the process of machining carbide saw blades. By investigating the influence of different addition amounts of glass fiber and platinum disulfide on the performance of the grinding wheel, the quality of the machined workpiece is affected. The optimum addition amount is 7.5 vol% of glass fiber and 5 vol% of platinum disulfide. The surface roughness and brightness of the workpiece processed by the hardwood woodworking saw blade prepared by this formula can meet the requirements of high-end customers, and the comprehensive service life of the grinding wheel. Increase by 30% to 67%. The preferred grinding wheel not only has a direct effect on the hard alloy woodworking saw blade, but also has a certain reference effect on the saw blade processing in other industries.
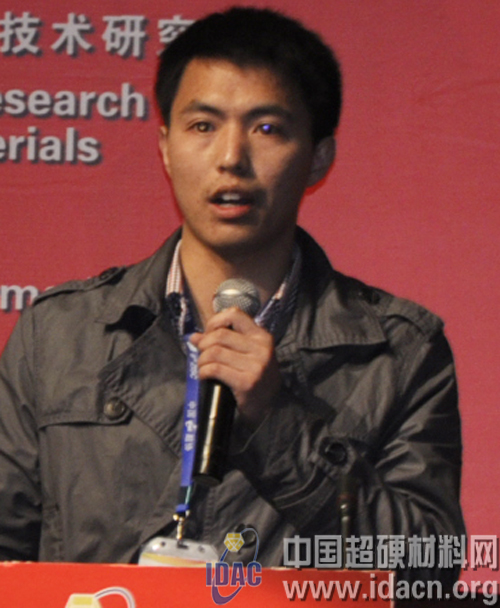
Study on Wear of Diamond Grinding Wheel of Ultrasonic-assisted Grinding of SiC Ceramics
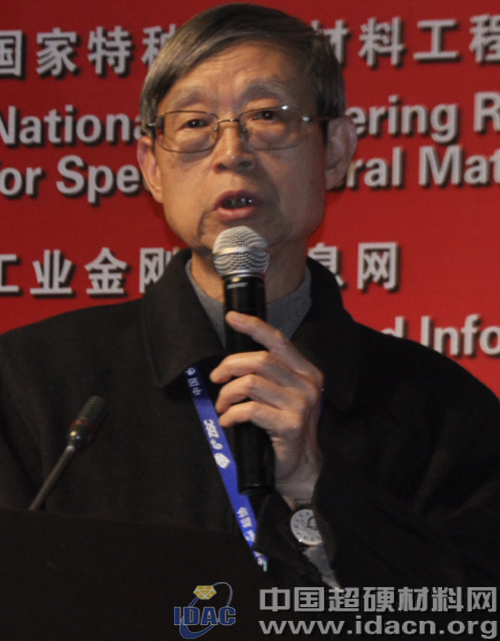
Nano diamond anti-friction and anti-wear effect
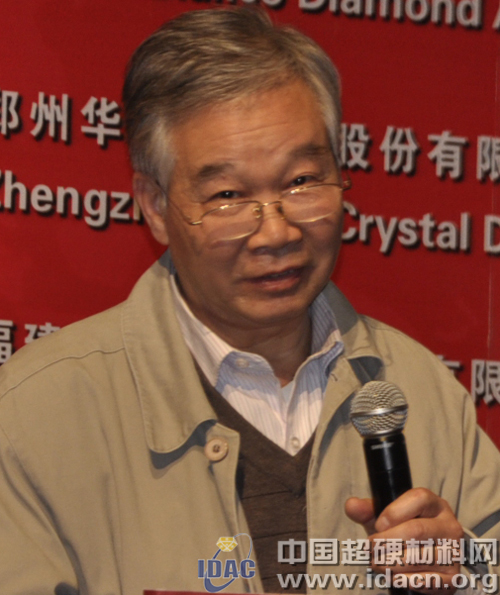
The understanding and practice of diamond bit research
The report analyzes the problems that have arisen in drilling engineering in recent years. Based on the hotspots in the research and application of hot-pressed diamond drill bits, it is based on practice and summarizes some insights. The application of cold press forming and granulating technology and the sintering process combining cold pressing and hot pressing methods are proposed. The design idea of ​​drilling hard and compact rock drill bit is put forward, and the design and manufacturing method of replacing the electroplated drill bit with hot pressing bit is proposed. . At the same time, it is believed that the performance of the drill bit, the nature of the rock and the drilling process technology are inseparable systems; the design and selection of the drill bit is inseparable from the nature of the rock and the drilling process technology. These conclusions are useful for both the drill manufacturer and the user.
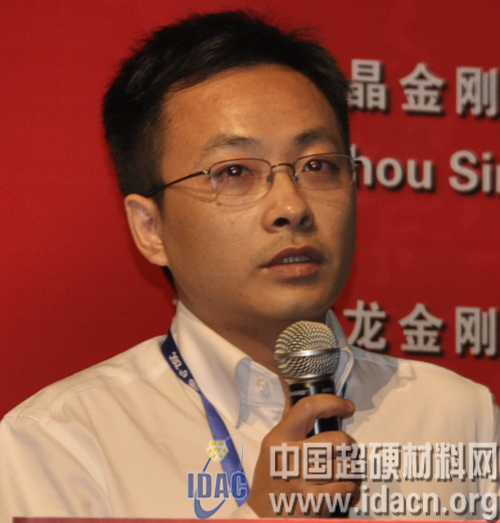
Preliminary study on formulation design of deep hole drill bit under new process conditions
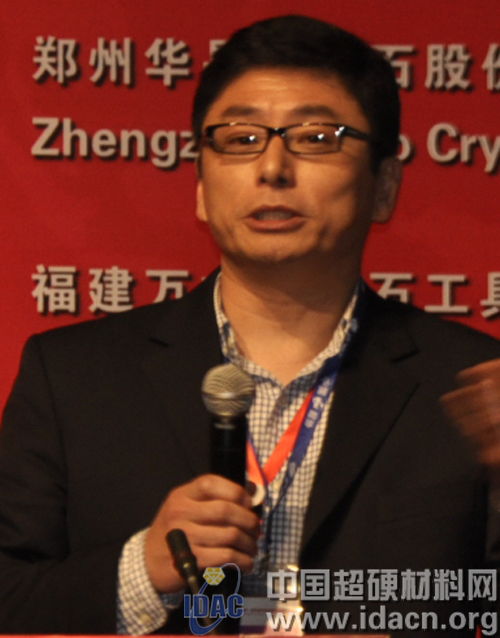
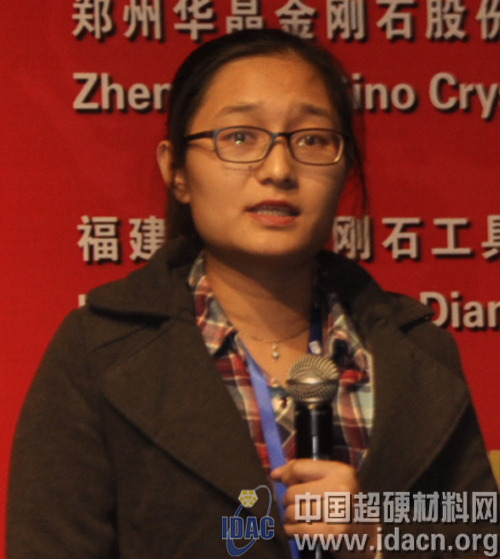
Study on the Influence of Different Iron Powder on the Performance of Diamond Grinding Blocks
The report uses electrolytic iron powder, hydroxy iron powder, P-Fe powder, reduced iron powder, white cast iron powder and gray cast iron powder to prepare diamond grinding blocks to grind ceramic floor tiles with sharpness. And wear time shows a big difference. The reasons for these differences are analyzed and it is believed that the selection of reasonable iron powder can significantly optimize the performance of diamond grinding blocks.
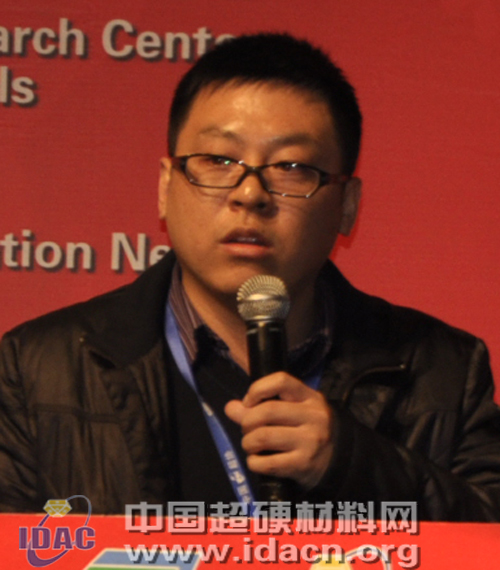
New progress in pressure control technology for six-face press
This report focuses on the new developments of domestic six-face presses in supercharged source, overpressure and pressure relief technology in recent years. The principle and application of double-acting reciprocating supercharger are analyzed in detail, showing the proportional overflow. The principle of valve and proportional flow valve in overpressure speed control, the application of proportional stop valve in slow pressure relief is analyzed.
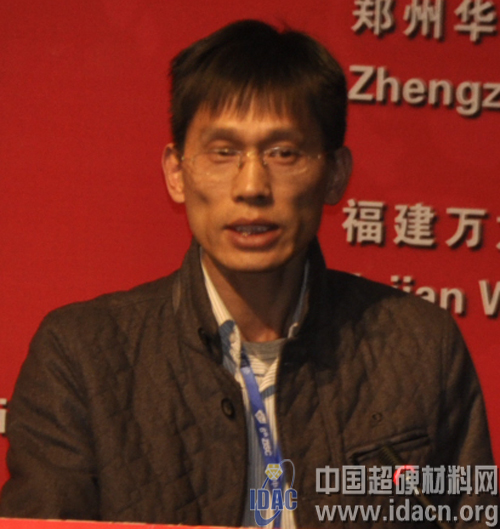
Optimization analysis based on Ansys Workbench six-face press
First, use the SolidWorks software to establish a three-dimensional solid model of the hinge beam system according to the design requirements. Secondly, the finite element analysis model is established in ANSYS Workbench software and the static analysis is carried out. The stress distribution and deformation of the diamond press structure under working conditions are obtained. Thirdly, the model is converted into a parametric model and imported into ANSYS Work-bench. Through the analysis of the structural characteristics and stress of the hinge beam, the main volume is selected by the stress value of the part volume and several stresses. The structural dimensions are design variables (such as the bottom chamfer of the cylinder, the thickness of the lug, the distance between the two lugs, and the chamfering of the upper and lower lugs), so as to reduce the stress without increasing the amount of material. value. Finally, to reduce the stress concentration at the joint between the lug and the cylinder, add two rounded corners at the joint and optimize the radius of the two corners.
The report provides an accurate and reliable design method for the development of the new diamond six-face press. With the CAE platform of ANSYSWorkbench, it helps to improve the design and analysis level of mechanical parts, shorten the development cycle and save costs, which is of great significance for the design and improvement of diamond presses.
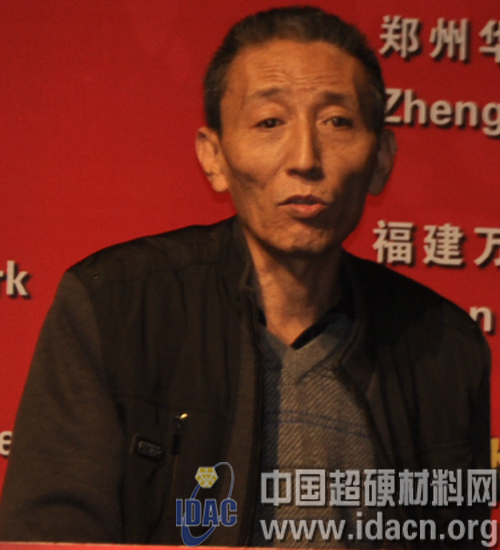
Introduce a fine particle shaper
With the development of global technology, the application of diamond has evolved from traditional geological drilling and stone cutting to more and more industries, such as aerospace, airship, high-speed railway, automobile manufacturing, semiconductor, solar energy, etc. The demand is growing rapidly. In the past, China imported a large amount of foreign products because of the lack of such varieties. Nowadays, several large diamond manufacturers in China have been able to produce fine particles (400~1200 mesh) of diamonds in batches after years of research and development. The author's company learned through investigation that the company that produces such diamonds can only use the original model to perform multiple selections because there is no suitable shape selection equipment for fine particles. However, the effect is still not satisfactory, especially It is basically 600 years to select the shape, the phenomenon of mixing is very serious, so that the business sales, especially the product price is greatly affected, and a new type of equipment is urgently needed to solve the above problems.
To this end, our factory has set up a research team since 2009 to develop a shape selection machine specially designed for the selection of fine-grained diamonds. This article introduces the performance, technical indicators and some details of the development of the machine to everyone.
Application of PCD cutter in CFRP composite processing
Preparation and properties of tung oil modified phenolic resin abrasive tools
Experimental study on diamond film deposited by razor blade
Development and current status of diamond composite sheets (PDC) for oil drilling
Study on Properties of Cutting Titanium Alloy TC4 with Different Bonding Agent PCBN Tools
High temperature rapid vulcanization improves the production efficiency of diamond rubber wire saw
Application of X-ray Fluorescence Spectroscopy in the Production of Diamond Tools
National strategy is based on active development of deep hole drilling
Study on the Influence of Multi-Particle Mixing System of Same-Type Fe Powder on the Performance of Pressureless Sintered Diamond Circular Saw Blade
Study on improving transition layer formulation to reduce sintering temperature and reduce laser welding pores
Effect of particle size of carbonyl iron powder on press formability of sintered diamond circular saw blade
China Compression Springs Stainless Steel Compression Spring
Compression Springs,Heavy Duty Compression Springs,Stainless Steel Compression Springs,Metal Springs Compression
applicaiton: viation,automotive, motorbike, bicycle, automatic equipment, household appliance, medical device ,toy, telecommunication,computer, instrument and meter,furniture, electric tools,mold and other industries
China leading manufacturers and suppliers of Compression Springs,coil spring,compress spring coil,Heavy Duty Compression Sprins,Stainless Steel Compression Spring,Metal Compression Spring, etc.
coil spring,compress spring coil,Heavy Duty Compression Sprins,Stainless Steel Compression Spring,Metal Compression Spring
Shenzhen Lanejoy Technology Co.,LTD , http://www.wirefruitbasket.com