The collection and treatment of flammable and explosive dust has always been a difficult point in industrial ventilation and dust removal. It should also be a focus that deserves attention. This requires not only the practitioners to have more comprehensive business knowledge, but also a highly rigorous and responsible attitude. Indispensable. What is flammable and explosive dust, the on-site staff must have a clear understanding of the materials they handle, there are a lot of information to check, there are many documents to refer to, the key is to have a deep understanding of the actual dust production process, dust The physical and chemical properties of the dust body give a precise definition, so that the design of the dust removal system, the selection of equipment and the responsibility of manufacturing applications can be carried out accurately.
Dust generated in metal processing may cause burning or even explosion. The concept of combustion and explosion is different. First, let's talk about combustion. It refers to the exothermic reaction of combustibles and oxidants, usually accompanied by flame, luminescence, and fuming. Combustion of matter requires three elements at the same time, namely, flammable substances, combustion-supporting substances and sources of ignition. Three defects are unlikely to cause combustion. For example, in the process of plasma cutting and laser cutting some alloy sheets, the generated soot is flammable, and the ubiquitous oxygen is a combustion-supporting substance. At this time, there are open flames, electric sparks, even sparks and heat generated by friction and impact in the environment. And physical and chemical factors such as oxidation heat that causes spontaneous combustion can become a source of ignition. Measures are taken to prevent the three elements from being present at different times. For example, the use of high-efficiency precipitator devices to collect and control combustibles, reduce or isolate air into the dedusting process system, and prevent and eliminate sources of ignition can prevent combustion from occurring, thereby achieving fire prevention and disaster relief.
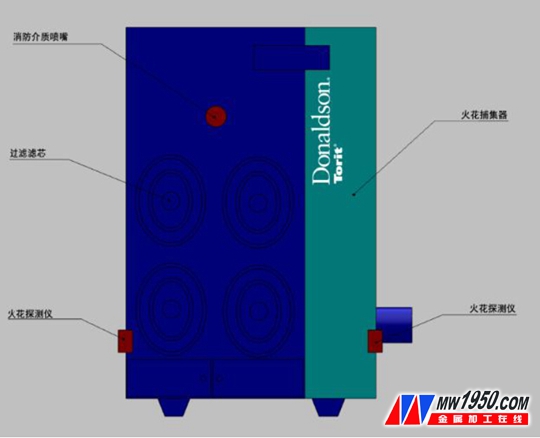
Spark detection and extinguishing system installation diagram
However, such ideal measures and conditions are often destroyed due to improper management or mishandling of equipment, causing unpredictable fire disasters. The spark detection and extinguishing system is one way to reduce this damage. The working principle is: detecting the occurrence of sparks in the initial stage of the precipitator, promptly issuing an alarm through the detector, automatically or manually opening the fire extinguishing agent injection system, and the possible end of the fire in the germination state, thereby achieving the effect of fire prevention, Reduce unnecessary losses and avoid the risk of further explosions. After the spark extinguishing process is completed, the dust collector equipment needs to be cleaned and repaired before it can be put into production again.
The spark detector is installed on the wall of the device and connected to the controller. When the detection signal is received, the alarm will be triggered quickly, indicating that the extinguishing system will spray the fire extinguishing medium in the dust collector, such as spraying water, spraying nitrogen or spraying carbon dioxide gas, and extinguishing the fire in time. Burning body such as flame or ash. Note that water collectors that collect dust of special properties such as aluminum powder cannot be sprayed with water, have a strong oxidative exothermic reaction and support combustion, and can only be extinguished by spraying nitrogen, carbon dioxide, or other selective inert gas.
In the production of some metal parts grinding, polishing and drawing, the amount of dust generated is sometimes large, and environmental pollution not only poses a threat to the health of workers, but also has the hidden danger of personal safety caused by explosion. In recent years, such explosions and personal injuries have been reported in some places, which cannot but cause concern in all aspects of society. The consequences of such an explosion are more violent than the burning of the fire, and the damage is even more devastating. An explosion is a phenomenon in which energy (physical or chemical) is rapidly released or rapidly converted into mechanical work and other energy. In general, the explosion phenomenon has the following characteristics: 1) the explosion process proceeds quickly; 2) the pressure near the explosion point rises sharply, most of the explosions are accompanied by an increase in temperature; 3) the surrounding medium vibrates under pressure or is subjected to mechanical Destruction; 4) Sound due to vibration of the medium. Among them, the sharp increase in pressure is the most important feature of the explosion phenomenon. The primary condition for a dust explosion is that the dust itself can ignite, that is, it can oxidize with oxygen in the air. Such as coal dust, aluminum powder, metal alloy powder, flour and cotton dust; secondly, the dust suspended in the air reaches a certain concentration (beyond its lower explosion limit). The dust is suspended to ensure that the surface is in sufficient contact with air (oxygen), and the accumulated dust does not generally explode; in addition, there must be enough initial energy to cause the dust explosion. As long as the above conditions are met, it will cause dust explosion.
The types of explosive dust in the air may include: 1) metals such as molybdenum, niobium, silicon, zirconium, iron, ferrosilicon, magnesium, aluminum-magnesium alloy, etc.; 2) synthetic materials such as plastics, synthetic resins, synthetic cellulose. , organic chemical raw materials, cellulose floc; 3) food products, such as flour, starch, sugar, etc.; 4) industrial raw materials, such as coal powder, wood, dry pulp. The dust explosion index (Kst) value is one of the main basis for the design of ventilation and dust removal engineering. At the same time, the minimum concentration that can cause the explosion, that is, the lower explosion limit (in g/m3), should be specified. Generally speaking, the smaller the dust particle size, the lower the lower explosion limit; the higher the oxygen concentration, the lower the lower explosion limit; the higher the flammable volatile content, the lower the dust explosion lower limit. The concentration of such substances in the ventilation and dust removal equipment and pipes should be controlled below 50% of the lower explosion limit. By reducing the effects of the explosion, the residual pressure is below the pressure level of the process equipment. The maximum explosion pressure (Pmax) is typically above 100 psi and the set residual pressure (Pred) is typically less than 3 psi.
The dust explosion index (Kst) is the product of the maximum explosion pressure rise rate and the cube root of the container volume in a 1 m3 closed vessel. It is used to indicate the severity and danger of dust deflagration. The larger the Kst value is. The higher the risk.

For the dust explosion that may occur in the dust collector or ventilation duct, it is a relatively effective measure to adopt the explosion suppression and chemical isolation system. The design principle of explosion suppression: the early signs of the onset of the explosion are detected, and the explosion prevention effect is achieved by rapidly spraying the chemical fire extinguishing agent into the developing fireball to completely end the burning phenomenon. After the suppression process is completed, a quick cleaning can be performed to allow the production to proceed again. The explosion suppression system includes an accurate sensor that will detect the pressure wave at the initial stage of the explosion (which is always faster than the speed of the fireball). The sensor should be designed to prevent false starts due to vibration or other non-explosive pressure wave events. An electrical signal from the sensor activates a "firearm" mounted on the surface of the device to directly spray food grade NaHCO2 fire extinguishing agent into the equipment. The fire extinguishing agent is effectively sprayed through the nozzle, and the extinguishing has not formed a source of deflagration. Depending on the conditions of use of the precipitator, the system typically limits the pressure to within 0.2 bar. Studies have shown that an unprotected dust explosion can usually reach a minimum pressure of 8 bar in 1/4 second (different flammable dust pressure values ​​vary).
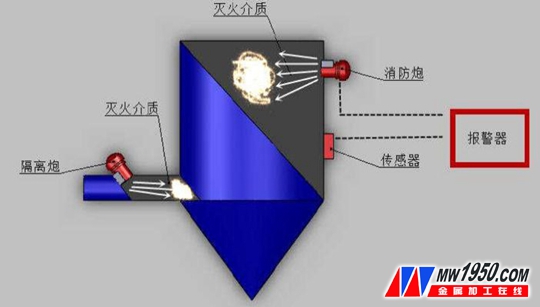
Chemical suppression arrangement diagram
The following figure shows an installation example. The work site completes the connection of the mechanical, pressure gas tank and all electrical port wiring of the system, ensuring the "system start alarm" is turned on correctly, the on-site emergency stop brake, monitoring the local AC power connection, The system startup diagnostic mode, system startup activation mode, etc. are normally stable and reliable. System operations at the job site should be completed with a complete continuous inspection record for operational analysis and, if necessary, for inspection.
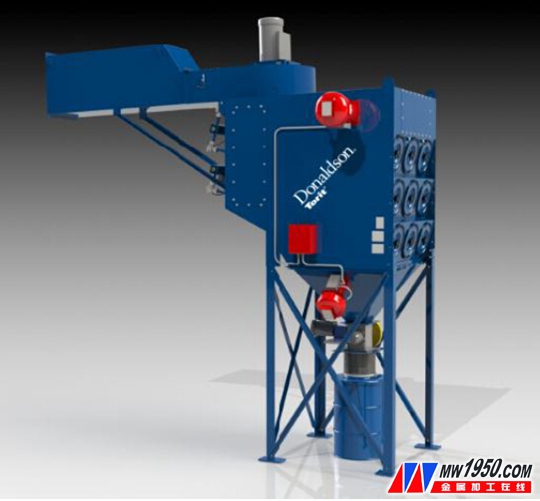
One of the easiest and most common methods for explosion-proof ignition of dust collectors is to use a venting diaphragm. The design considerations include the environment in which the equipment is installed, the direction of the venting port, the pressure resistance of the dust collector housing and its piping. Its advantages are lower cost, easy installation, no need for routine maintenance and monitoring; the disadvantage is that the venting diaphragm will be completely exploded and damaged, new parts and repairs need to be replaced, and the internal and surrounding environment of the equipment after partial explosion We do cleaning, and we are not able to cope with the fire that has formed a fireball. The design and calculation of the strength and size of the venting diaphragm matched with different types of dust collectors is critical, otherwise it may cause frequent venting actions, or the venting action may lag and delay the rescue.
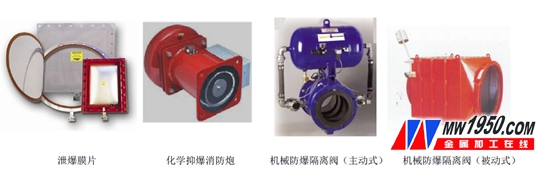
Some explosion-proof requirements require particularly strict working conditions, such as in the production of alloy parts grinding and metal parts thermal spraying process, it will also be combined with mechanical explosion-proof and chemical explosion-proof applications, while the mechanical explosion-proof valve segment is closed in time. , cut off the possibility of fire extension. Dust collected in dust collectors or pipes is often raised by the initial explosion, causing a new "secondary explosion". Because of the higher concentration of suspended dust at this time, the secondary explosion is more destructive and lethal than an explosion. The incidents of casualties in many accidents are almost caused by secondary explosions, so the prevention of secondary explosions is particularly important, and measures and means should be quick and reliable.
The following figure shows the fire suppression flowchart of the metal thermal spray dust removal system. It adopts the chemical extinction and mechanical explosion-proof valve linkage application method. At the same time, it also installs a venting diaphragm on the dust collector body. Does every point need to be worthwhile? Businesses, when there are conditions, it is safe and secure. Both the chemical extinguishing gun and the mechanical explosion-proof valve require accurate and reliable control triggering of the transmission signal of the professional detector, and the system response speed is the most basic requirement.
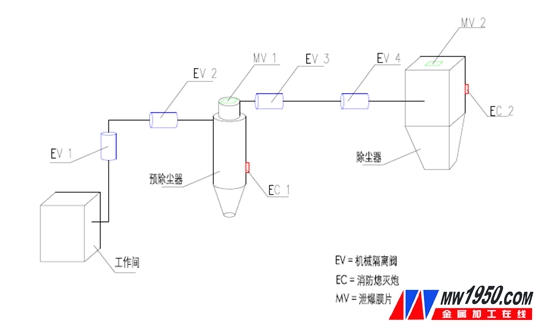
When considering the fire suppression system of the ventilation and dust removal system, there are other aspects that should be explored, such as the explosion-proof requirements of the fan motor and electrical control, the flame retardant capacity of the filter material, the anti-static performance, the grounding conduction problem of the dust collector, and the spark of the air inlet. The form of the plucking device, etc., must be added in place if necessary. Peripheral equipment such as suction hoods and pipes that constitute the ventilation and dust removal system should be scientific and reasonable, correctly designed, manufactured and installed, and can be put into production only after the commissioning and running standards are met.
It should be emphasized that after properly designing and installing the explosion-proof and explosion-proof facilities of the ventilation and dust removal system, the level of production operation management should also be improved, keeping the work site environment clean and thoroughly removing the flammable and easy generated during processing. Explosive dust, and strive to reduce the chance of detonation from the source.
Explosion-proof equipment for flammable dust explosions has always been strictly regulated by laws and regulations. The National Fire Protection Association (NFPA) has developed a series of standards for the protection and prevention of explosions; the ATEX directive is the corresponding standard commonly used in Europe, which stipulates the technical requirements for equipment in explosive environments, only ATEX is obtained. Explosion-proof equipment can only be sold and used in these countries after certification. China also has sound national standards and norms, such as dust explosion safety regulations (GB15577-2007), dust explosion pressure relief guidelines (GB15605-2008), dust explosion detectors for dust explosion hazardous areas (GB/T17919-2008) and many more. In particular, on August 2, after the explosion of the Kunshan Metal Factory, the State Administration of Work Safety issued the No. 68 Order “Strictly Prevent Five Dust Explosions of Enterprisesâ€, further clarifying the importance of industrial dust dust explosion-proof and fire safety and the standard Implementation requirements. It is hoped that through experience and lessons, China's industrial dust removal field will receive due attention, supervision and management of enterprises and enterprises will be strengthened, and the technical level will be continuously improved.
UFO Highbay Light
We diviided the led light according to the using eviiroment. Most of our product is the commercial LED Lighting
Commercial lighting is a term used to describe lighting that is used in commercial spaces, including auto dealerships, distribution centers, churches, factories, offices, and warehouses. Unlike residential lighting, commercial lighting is made to withstand more abuse and has a longer lifespan.
While the focus of residential lighting is often on aesthetics, commercial lighting is task orientated. Commercial lighting systems are designed based on what the application is. For example, in an office-type setting, you may see task lighting, which illuminates specific areas where employees need concentrated light to be able to perform their jobs.
Ufo Highbay Light,Industrial Led High Bay Light,Led High Bay Lights 200W,Ufo Led High Bay Light 150W
Jiangmen Dilin Lighting High-Tech Co., Ltd. , https://www.jmdilinled.com